Real Info About What Is The Acceptable IR Value

IR Values And Identifying Diagram Quizlet
Understanding Acceptable IR Values
1. What's the Big Deal with IR Values Anyway?
Alright, let's talk IR values. No, I'm not talking about infrared blasters (though those are pretty cool). In this case, IR stands for Insulation Resistance, and it's a measure of how well an electrical circuit's insulation is preventing current from leaking where it shouldn't. Think of it like this: your electrical wiring is like a water pipe, and the insulation is what keeps the water (electricity) flowing inside the pipe, instead of spraying all over the place. A good IR value means the insulation is doing its job properly, keeping the electricity where it's supposed to be. Think of a worn garden hose with a bunch of leaks; that's what we're trying to avoid here!
Why should you care? Because a low IR value can mean a potential safety hazard. It indicates that current is leaking, which can lead to shocks, fires, and equipment failure. Not exactly the kind of excitement you want in your day, right? Regular insulation resistance testing is a crucial part of preventative maintenance, helping to identify potential problems before they become major disasters. Plus, its often mandated by safety regulations to ensure electrical systems are operating safely. So, while it might seem a bit technical, understanding IR values is essential for anyone dealing with electrical systems.
So, what contributes to a low IR value? Well, it can be a number of things. Moisture is a big culprit. Dampness reduces the insulation's ability to resist the flow of current, almost like water weakening the walls of our imaginary pipe. Contamination, such as dust, dirt, or chemicals, can also create conductive paths that allow current to leak. Physical damage to the insulation, like cracks or abrasions, is another common cause. And sometimes, insulation just degrades over time due to heat, age, or other environmental factors. It's like anything else, it wears out!
Now, imagine you're a doctor checking a patient. You wouldn't just poke them and say, "Yep, you're sick!" You'd take measurements, run tests, and compare the results to a standard range. Similarly, with IR values, we need a benchmark to know what's acceptable and what's not. That's where the standards come in. Organizations like the IEEE (Institute of Electrical and Electronics Engineers) and the NETA (InterNational Electrical Testing Association) provide guidelines for acceptable IR values based on factors like voltage, equipment type, and operating conditions. Following these standards is crucial for ensuring accurate and reliable results.
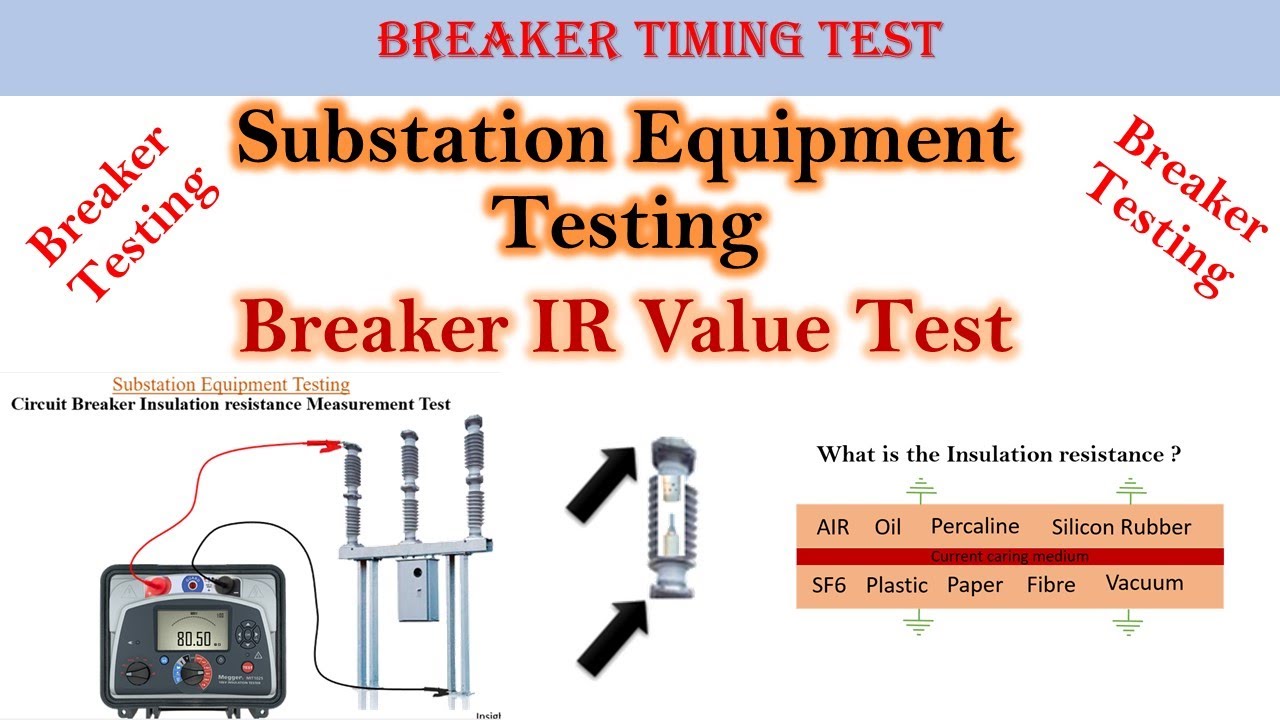
Circuit Breaker IR Value Test Hindi YouTube
Determining Acceptable IR Values
2. What's a "Good" IR Value, Anyway?
Alright, let's get down to brass tacks: what numbers are we looking for? Here's where it gets a bit less straightforward, because the "acceptable" IR value isn't a one-size-fits-all kind of deal. It depends on several factors, including the voltage rating of the equipment, the type of insulation material used, and even the operating temperature. But generally speaking, higher is better. A higher IR value indicates better insulation resistance, meaning less leakage current and a safer, more efficient system.
As a general guideline, many standards recommend a minimum IR value of 1 megohm (1 million ohms) for low-voltage equipment. Think of it as a starting point. For higher-voltage equipment, the minimum acceptable IR value typically increases proportionally with the voltage. For example, you might see recommendations of 1 megohm per 1,000 volts. But remember, these are just guidelines. It's always best to consult the manufacturer's specifications or relevant industry standards for the specific equipment you're testing. Always double check to prevent costly errors.
It's also crucial to consider the environmental conditions. Temperature and humidity can significantly affect IR measurements. Higher temperatures generally decrease insulation resistance, while high humidity can introduce moisture, also lowering IR values. That's why it's important to record the temperature and humidity at the time of testing and to correct the measurements accordingly, if necessary. Failing to account for these factors can lead to inaccurate results and incorrect conclusions. It's like trying to bake a cake without accounting for the oven temperature!
To further complicate matters, different types of equipment have different IR value requirements. A motor, for example, might have a different acceptable IR value than a transformer or a cable. That's because each type of equipment has its own unique insulation characteristics and operating conditions. Again, the best approach is to consult the manufacturer's specifications or relevant industry standards for the specific equipment you're testing. Look up the proper value for each application; don't assume they are all the same.
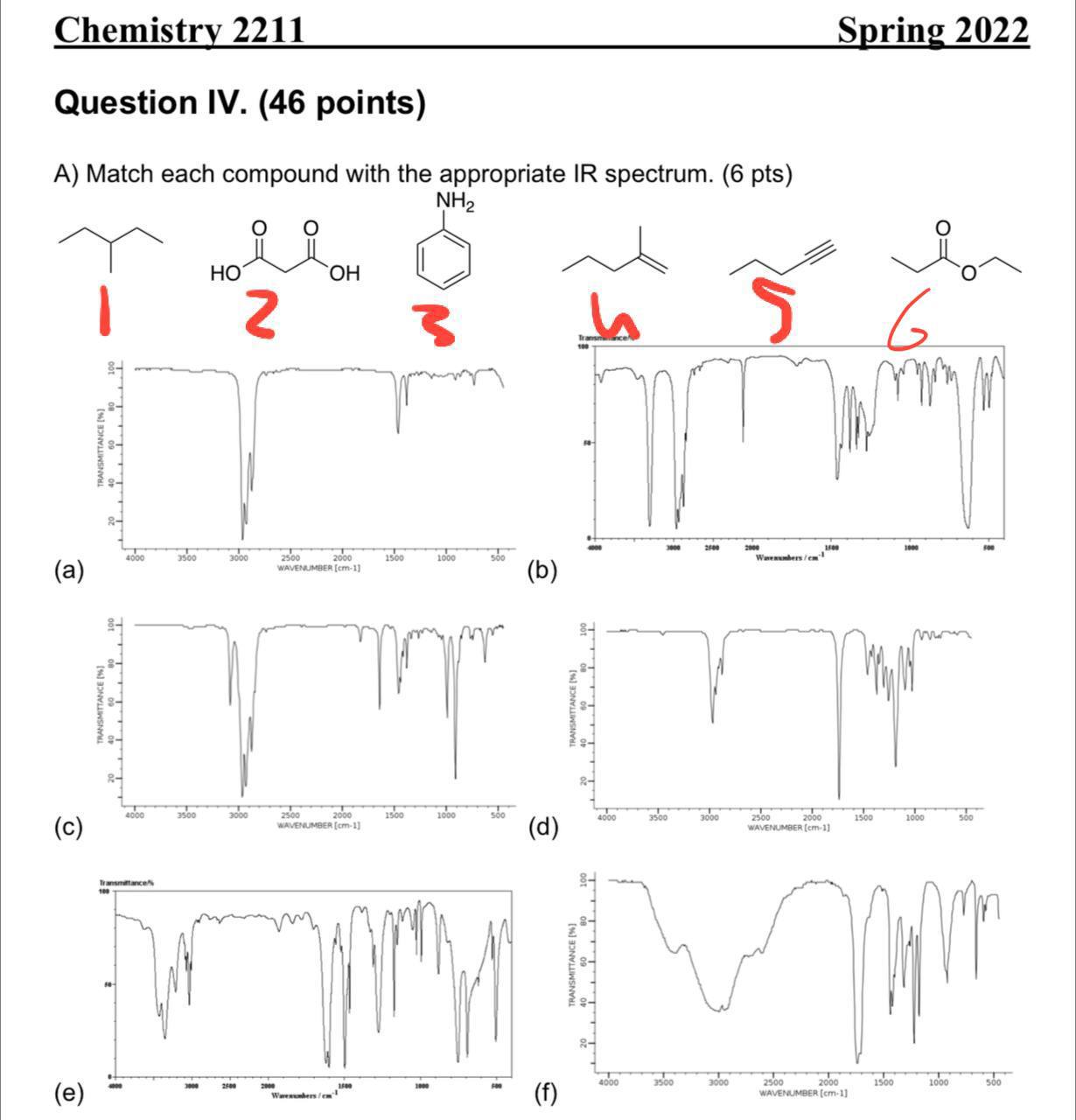
Factors Influencing IR Values
3. Digging Deeper
So, we know that moisture, temperature, and contamination can affect IR values. But there's more to the story. The type of insulation material plays a significant role. Different materials have different inherent insulation properties. For example, cross-linked polyethylene (XLPE) insulation generally has higher insulation resistance than older materials like rubber or paper. The age of the insulation is also a factor. Over time, insulation materials can degrade due to heat, oxidation, and other factors, leading to a decrease in insulation resistance. This is just a natural part of the life cycle of the materials involved.
The applied voltage during the IR test can also influence the results. Higher test voltages can sometimes reveal weaknesses in the insulation that might not be apparent at lower voltages. However, it's important to use the correct test voltage, as excessive voltage can damage the insulation. The recommended test voltage is typically specified in the manufacturer's specifications or relevant industry standards. Using the wrong test voltage can lead to inaccurate results or even damage the equipment, so always follow the guidelines.
Another factor to consider is the condition of the equipment. If the equipment has been exposed to harsh environments or has been subjected to mechanical stress, the insulation may be damaged, leading to a lower IR value. Look for any signs of physical damage, such as cracks, abrasions, or discoloration. These are red flags that the insulation may be compromised. Addressing these issues early on can prevent more serious problems down the road. Prevention is better than cure in this case.
Finally, the test equipment itself can affect the results. It's important to use a calibrated and properly functioning insulation resistance tester. A faulty tester can give inaccurate readings, leading to incorrect conclusions. Regular calibration ensures that the tester is providing accurate and reliable results. Additionally, it's important to follow the manufacturer's instructions for using the tester. Using the tester incorrectly can also lead to inaccurate results.
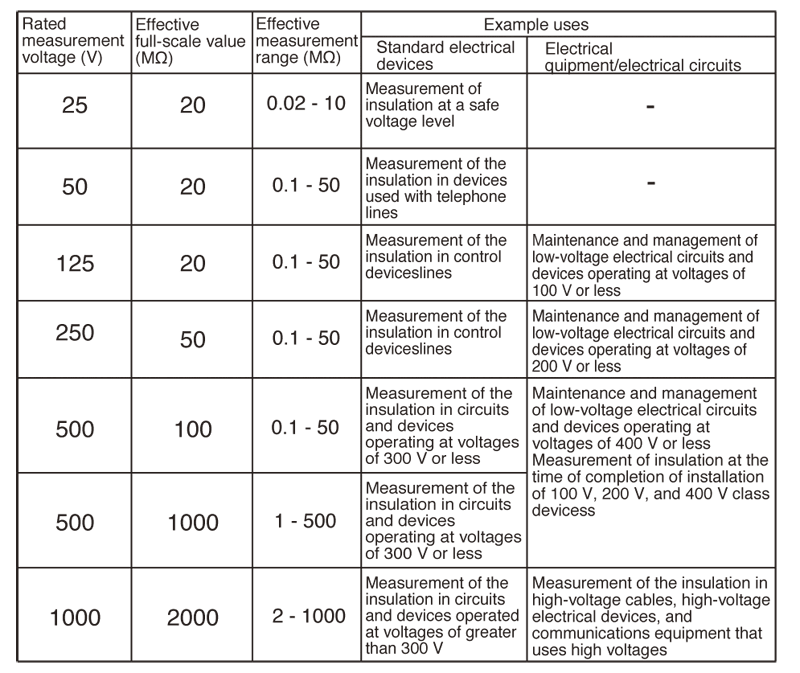
What Is Insulation Resistance Testing? Hioki
Performing an IR Test
4. Step-by-Step Guide to IR Testing
Okay, so you understand what IR values are and what influences them. Now, how do you actually measure them? First, safety first! Always de-energize and lock out the circuit or equipment you're testing. This is absolutely crucial to prevent electric shock. Double-check that the power is off before proceeding. You don't want to become part of the circuit!
Next, isolate the circuit or equipment being tested. Disconnect it from any other circuits or loads. This ensures that you're only measuring the insulation resistance of the specific circuit or equipment you're interested in. Connecting to other circuits will skew the results and make them unreliable. Think of it like trying to weigh yourself while holding a bunch of stuff — you won't get an accurate reading of your actual weight.
Now, connect the insulation resistance tester according to the manufacturer's instructions. Typically, you'll connect one lead to the conductor and the other lead to ground or the equipment's enclosure. Make sure the connections are clean and secure. Poor connections can lead to inaccurate readings. Double-check your wiring before starting the test to avoid any mistakes.
Apply the appropriate test voltage as specified in the manufacturer's specifications or relevant industry standards. Let the test run for the recommended duration, typically one minute. This allows the insulation to fully charge and provides a stable reading. Record the IR value displayed by the tester. Compare the measured value to the acceptable IR value for the equipment you're testing. If the measured value is below the acceptable value, it indicates a potential insulation problem that needs to be investigated further.
Troubleshooting Low IR Values
5. Fixing the Problem
So, you've performed an IR test and the value is below the acceptable threshold. Don't panic! The first step is to verify the test results. Double-check your connections, the test voltage, and the tester's calibration. Make sure you followed the correct testing procedure. A simple mistake can sometimes lead to an inaccurate reading. Retesting can confirm the issue.
If the test results are confirmed, the next step is to identify the cause of the low IR value. Inspect the insulation for any signs of physical damage, such as cracks, abrasions, or discoloration. Check for moisture or contamination. Use a flashlight to get a good look at hard-to-reach areas. A visual inspection can often reveal the source of the problem.
If you suspect moisture, try drying the insulation with a heat gun or by leaving the equipment in a warm, dry environment for a period of time. Re-test the insulation resistance after drying. If the IR value improves, it confirms that moisture was the cause of the problem. Take steps to prevent moisture from recurring, such as improving ventilation or sealing the equipment.
If you suspect contamination, clean the insulation with a suitable solvent. Make sure the solvent is compatible with the insulation material and won't damage it. Re-test the insulation resistance after cleaning. If the IR value improves, it confirms that contamination was the cause of the problem. Implement measures to prevent contamination, such as regular cleaning or using filters. If the insulation is damaged, it may need to be repaired or replaced. Consult with a qualified electrician to determine the best course of action.
FAQ
6. Your IR Value Questions Answered
Q: What happens if I ignore a low IR value?
A: Ignoring a low IR value is like ignoring a persistent cough — it could lead to something much worse. It increases the risk of electrical shock, fire hazards, and equipment failure. It's always better to address the problem proactively rather than waiting for a disaster to strike.
Q: How often should I perform IR tests?
A: The frequency of IR testing depends on the equipment and the operating environment. Critical equipment should be tested more frequently than non-critical equipment. A good rule of thumb is to perform IR tests at least annually, but more frequent testing may be necessary in harsh environments or for equipment that is subjected to heavy use.
Q: Can I perform IR tests myself, or do I need a qualified electrician?
A: While some basic IR testing can be performed by trained personnel, it's generally recommended to have a qualified electrician perform IR tests, especially for high-voltage equipment or complex systems. A qualified electrician has the knowledge and experience to perform the tests safely and accurately, and to interpret the results correctly.